Advance knowledge of abnormal component wear means zero unplanned outages, lost revenue or secondary damage.
Bearing damage is the leading cause of unplanned events. MetalSCAN offers operators of engines, turbines, and gearboxes real-time data on critical component condition and equipment health by detecting and analyzing 100% of wear debris in oil flow.
MetalSCAN technology enables operators to maximize equipment availability, reduce risk, carry out predictive maintenance, extend overhaul intervals, predict component remaining life, and avoid secondary damage and costly equipment failures.
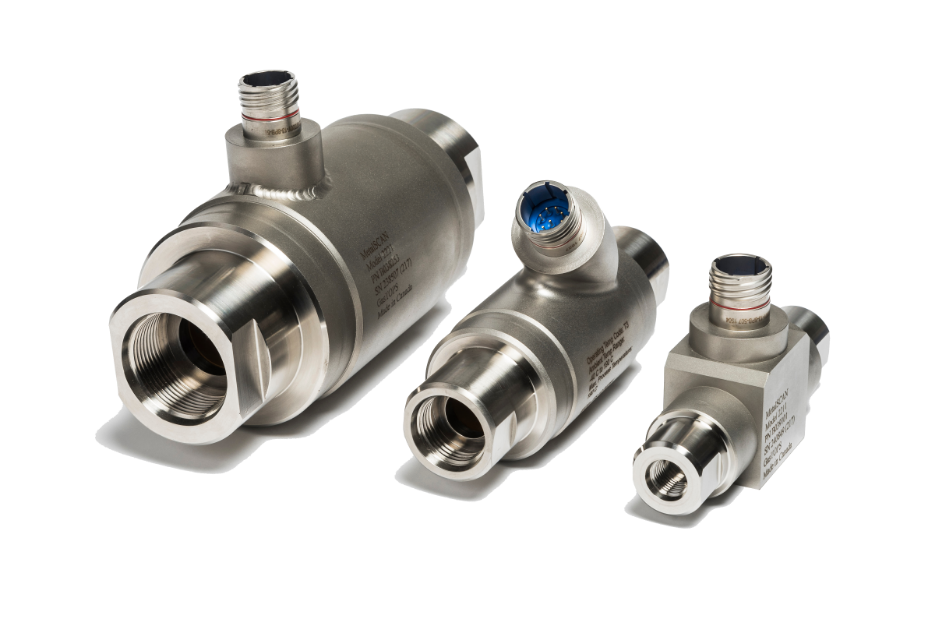
MetalSCAN enables real-time prognostics in condition-based maintenance (CBM) for critical oil-wetted components
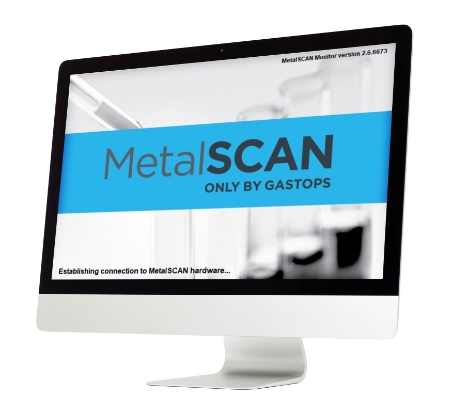
- Eliminate unplanned events & catastrophic failures
- Eliminate false and nuisance alarms
- Proactively plan maintenance for minimal disruptions
- Improve fault isolation, reduce troubleshooting times
- Avoid secondary damage
- Plan maintenance
- Extend scheduled inspections & maintenance intervals (on-condition)
- Reduction/elimination of routine oil sampling with enabling technology
How MetalSCAN Works
More than a particle counter, MetalSCAN is an online oil debris sensor that detects 100% of metal particles present in oil flow and compares damage progression to our proprietary statistical models. This wear debris sensor detects failure modes for critical components: bearings, gears, seals, and blades and identifies surface fatigue damage, build debris, and seal damage. Using this information, MetalSCAN provides real-time indication of severity and progression of damage. This oil debris sensor gives the earliest advance warning that equipment will require maintenance and estimates Remaining Useful Life (RUL).
MetalSCAN for Aerospace
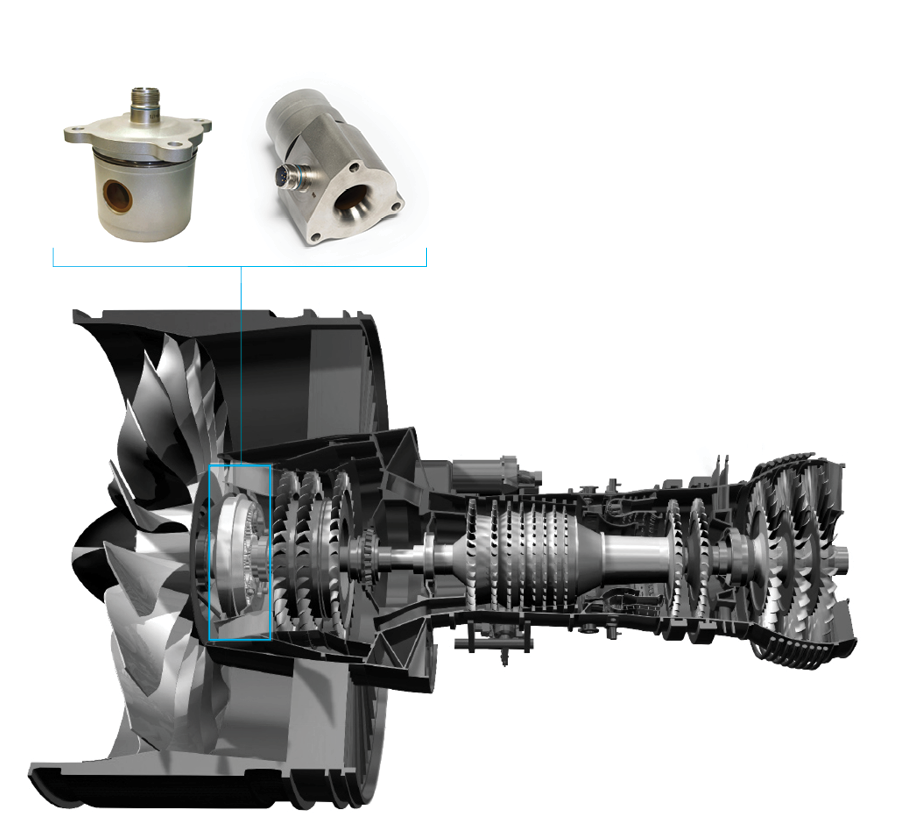
MetalSCAN is the alternative to notoriously unreliable chip detection systems which often fail to detect in-flight failures, unsafe operations, and mission abort events. Gastops originally developed MetalSCAN for the F-22 Advanced Tactical Fighter engine. Today, MetalSCAN is available for a wide range of military and commercial aircraft applications.
Real-time Prognostics
- Detect the onset of damage
- Measure health status
- Avoid in-flight failures and false indications
Proactive Detection of Service Needs
- Reduce maintenance and support costs
- Maximize mission readiness
- Improve reliability
Featured installations:
- Every Pratt & Whitney GTF commercial engine, including those flying on the:
- Airbus A320neo / PW1100G-JM
- Airbus A220 / PW1500G
- Embraer E-Jet 170 / PW1700G
- Embraer E-Jet 190 / PW1900G
- The world’s most advanced fighter jets including the:
- Lockheed Martin F-22 Raptor / PWF119
- Lockheed Martin F-35 Lightning / PWF135
- Lockheed Martin F-35 Lightning / 29,000HP gearbox on RR LiftSystem®
- Eurofighter Typhoon / EJ200
Product Brochure
Application Guides
MetalSCAN for Wind Turbines
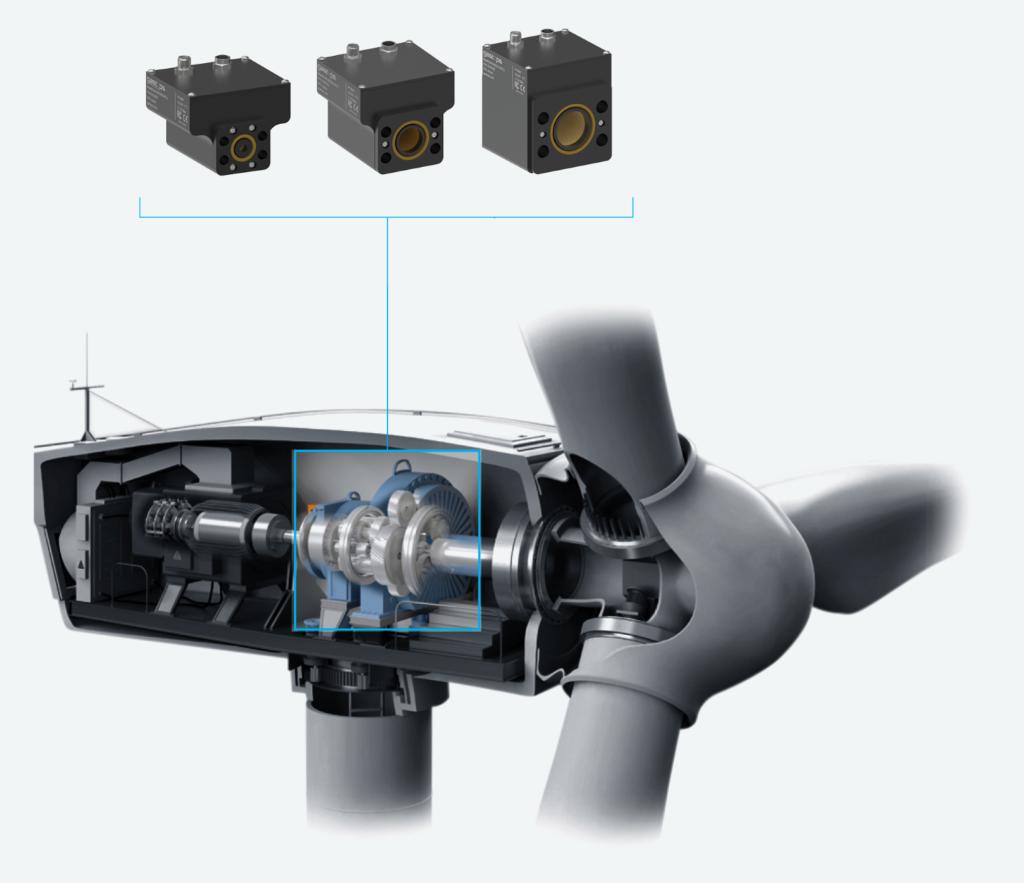
Designed specifically for wind turbine platforms, the MetalSCAN MS3500 oil debris monitoring system provides continuous monitoring of the gearbox.
MetalSCAN is a full-flow, non-obstructive, online debris detection system installed in the gearbox lubrication system. It detects the onset of surface fatigue of bearings and gears and tracks the progressive deterioration of the damage in real time, providing a continuous measure of gearbox condition.
Featured installations:
- Bill of Materials on all Vestas, Siemens Gamesa, GE and Nordex turbines
- A Standard Option on all new Vestas (non EnVentusTM), Siemens Gamesa, Nordex Group and GE wind turbines
- Major gearbox manufacturers including ZF, Winergy, Bosch Rexroth, Eickhoff, NGC and Moventas
- Turbine owners/operators including ENGIE, Orsted, Vattenfall, Statkraft, E.ON, EDP Renewables, Brookfield, Boralex, RWE AG and Iberdrola
MetalSCAN for Power, Compression and Marine Propulsion
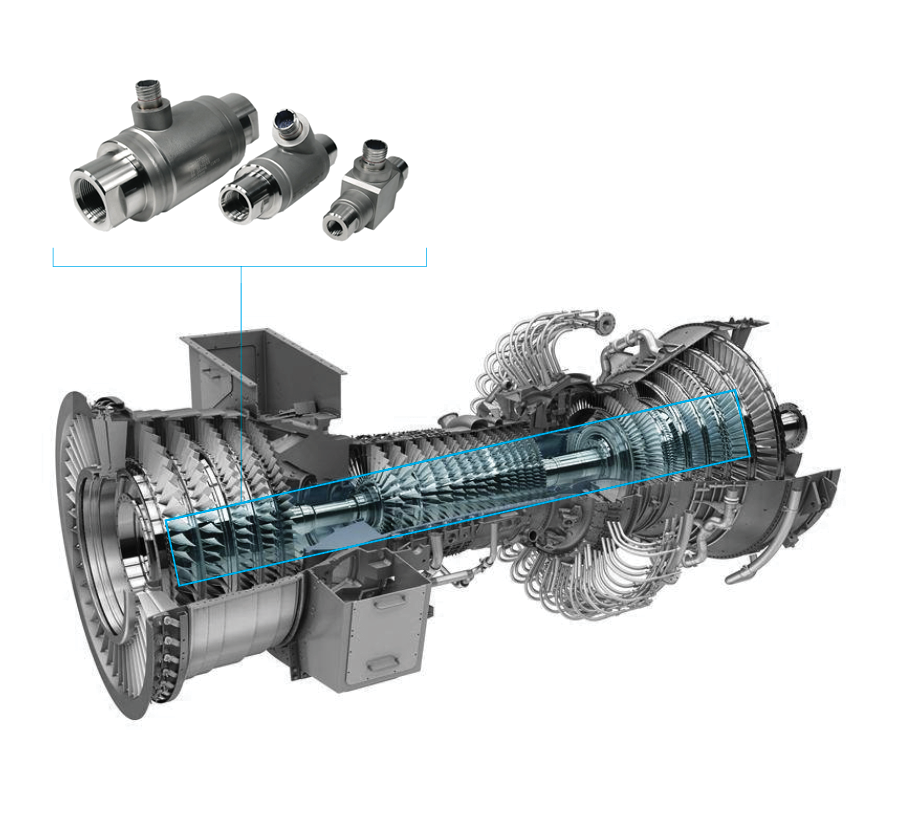
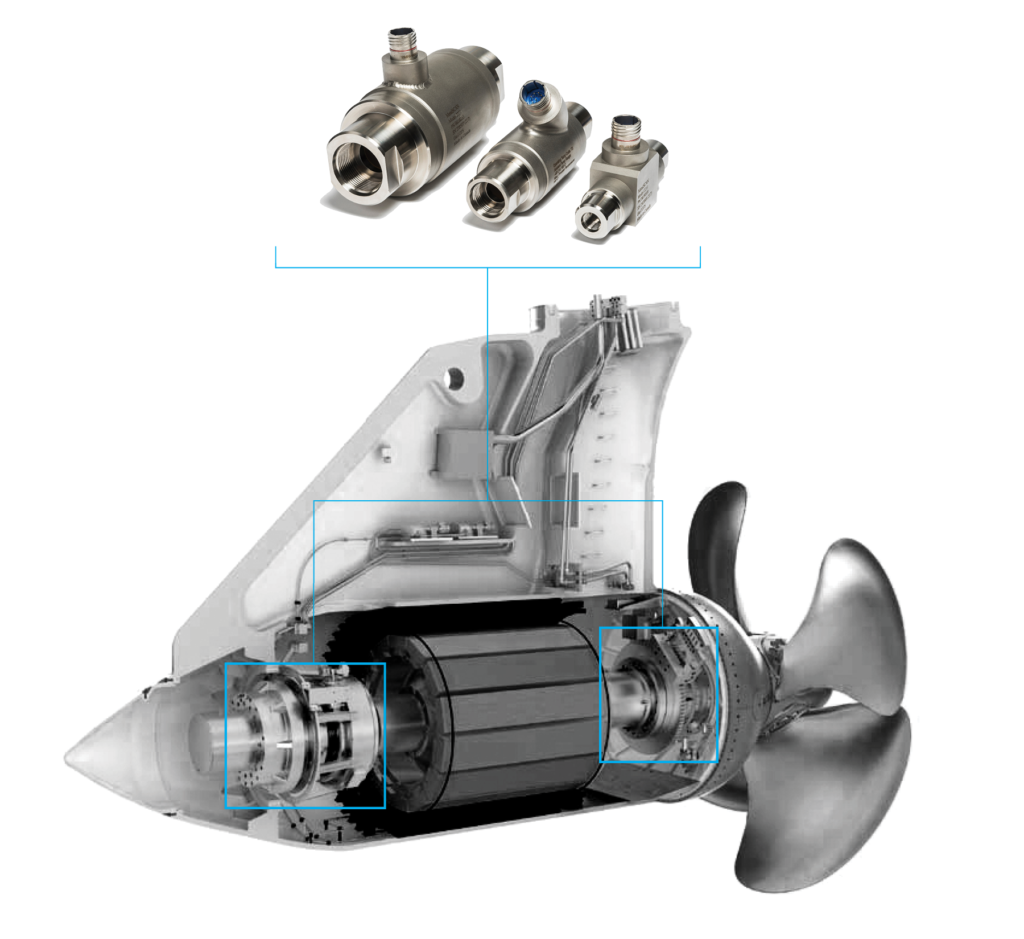
MetalSCAN MS4000/MS4110 are online oil debris monitoring systems designed to detect the passage of metallic particles in fluid lines. The systems, which can be used in any pipe flow situation, are particularly suited to equipment applications where detecting metallic debris in the lubrication oil can provide early indication of component damage.
MetalSCAN technology enables the operator to plan maintenance actions, thus reducing lost revenue and repair costs. It also optimizes equipment availability and proactive planning for required maintenance.
Features
- 100% detection of ferromagnetic (Fe) and non-ferromagnetic (NFe) metal particles
- Easy to install
- Easy to interpret
- Rugged, solid-state with no moving parts
- Full function continuous Built-in-Test (BIT)
- Proven reliability in harsh machinery, high temperature and hazardous environments
Featured installations:
- GE Energy LM9000, LM6000, LM5000, LM2500, LM1600 and LMS100, both new and in the aftermarket for power generation, compression and Naval Marine applications
- Mitsubishi Power Aero (Pratt & Whitney) FT4, FT8 and FT4000 both new and in the aftermarket for power generation and Naval Marine applications
- Siemens Energy/Rolls-Royce MT Avon, SGT-A05 (501K), Spey, SGT-A35 (RB211) and SGT-A65 (Trent), both new and in the aftermarket for power generation, compression and Naval Marine applications
- Monitoring all the Azimuth PODS designed and manufactured by ABB and Kongsberg Maritime that are propelling the world’s largest cruise ships, owned and operated by Royal Caribbean, Celebrity, Carnival, Norwegian and Star Cruise Lines
- Major industrial users include petrochemical companies such as SABIC and LANXESS, steel companies such as ArcelorMittal, and component manufacturers such as Bosch and Zanini Renk
